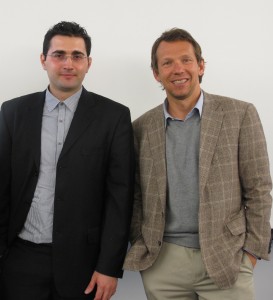
Picture your ideal mobile phone — it probably has a sleek design with a polished screen and a slim but fragile body. Now imagine that phone falling: either off the edge of your bed, out of the car as you open the door, or even clumsily out of your hand as you pull it out of your pocket. The sound and sight of a shattered screen that would likely follow are all too familiar, but what if there was a way to alter the properties of the materials used in our devices, our buildings, and the very infrastructure on which our lives are based? Yale researchers Professor Jan Schroers and Dr. Baran Sarac have tackled this question by developing a process to enhance the physical properties of a material utilizing “artificial microstructures.”
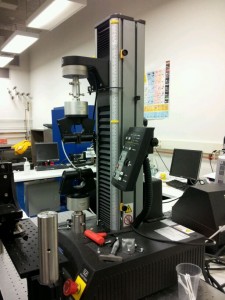
The Importance of Microstructures
Every material has measurable physical properties, such as tensile strength, ductility, and plasticity. These properties can be improved if a compatible microstructure is coupled with the desired material. Microstructures, which can only be seen using optical microscopes, can function to absorb stress, thus increasing a material’s strength and durability. The key features of microstructures include shape, size, volume, distribution, and spacing between each individual element. If a microstructure can be altered in a controlled manner to produce a structure analogous to a particular material, the material’s quality and durability can be greatly improved.
An example of the utility of microstructures is their role in improving the quality of refractory materials. Useful for the construction of industrial equipment such as kilns, incinerators, and reactors, refractory materials can withstand heat while retaining durability. Embedding microstructures in these materials greatly enhances their refractory properties. Furthermore, increasing the efficiency of materials decreases consumption and costs. For example, since 1970, the US has decreased its consumption, and by extension waste, of refractories by over 64 percent. And applications of microstructure-enhanced refractory materials are not only industry-related: for example, biomaterials (ex. hip replacements) to be used in vivo need to match in elasticity with the body parts they replace. The desired mechanical properties can be achieved via directed construction of microstructures. With such drastic improvements in sight, there is clearly incentive to further study and apply microstructures to more materials.
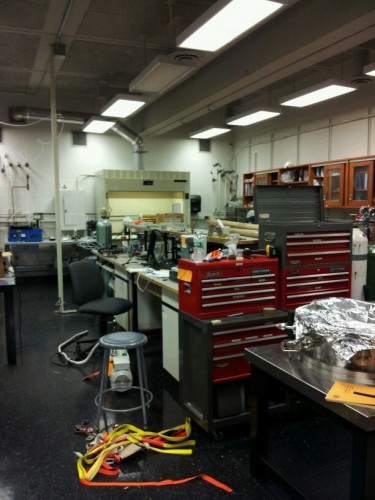
Introduction to the Project
Professor Schroers and his team used a class of material called Bulk Metallic Glasses (BMGs) for their study on microstructures. These materials mimic many properties of metals but are far more resilient and surprisingly plastic, or moldable. This unique conglomeration of properties makes BMGs promising in many areas of application from large structures down to nano-scale projects. Unfortunately, there is a barrier to the implementation of BMGs in improved materials: it has a gaping lack of tensile ductility, which prevents it from being worked into a desired shape without significant stress. This issue with what would otherwise be a perfect candidate for the future reshaping of materials was the focus for the “artificial microstructure” approach implemented by Schroers and his team.
The Process of Discovery
Schroers’ “artificial microstructures” approach is universally applicable to the study of all microstructures, and not only to BMGs. It strives to control individual characteristics of the microstructure independently, allowing isolated study and optimization of the properties of each microstructure within the overall material.
The technique of “artificial microstructures” has both a distinct process of generation and a unique method of implementation. Usually, microstructures are applied onto the material during the casting or heat treatment of the material. However, artificial microstructures are generated in a controlled manner on a template, and are then transferred to the metallic glass by reheating and pressing the material. This method of applying microstructures is more precise and efficient.
Schroers and his team analyzed the resulting heterostructure, a combination of material and microstructure, using three different methods: finite element simulation, a bending test, and heat treatment. The finite element simulation proved useful in modeling the mechanical behavior under stress. The bending test involved testing the behavior of the material in the elastic to plastic strain region and subsequently examining how the material changed in bending ductility in a range of strains. The heat treatment involved studying the heterostructure under varying annealing conditions and embrittlement to analyze thermal and structural properties for elevated temperature applications.
The project’s goal was to use the “artificial microstructures” technique to determine the factors in the microstructure that could imbue the BMGs with tensile ductility. The BMGs were studied in the soft, cellular phase, but the technique’s effect on the hardened, composite phase was also examined. By applying varying parameters to the microstructures, Schroers and his team found that the shape, volume, and interfacial strength projected qualities on the soft second phase that decreased shear stress in the composite phase. Furthermore, the spacing of the microstructures and the relative size of the overall material were also important in optimizing the tensile ductility and toughness of the BMGs. Overall, Professor Schroers and his team were able to identify a heterostructure that conferred tensile ductility onto the BMGs.
Implications and Further Studies
Materials are an integral part of everyday life, from the steel infrastructure of buildings and bridges to the polymer plastics that are used for garbage bins and kitchen appliances. The cost of production and waste from such usage of materials is also a significant part of daily life. The work of Schroers and Sarac has provided the industry with a new technique of improving the efficiency and quality of materials in a way that can be applied to decrease waste and increase cost-effectiveness.
Not only are BMGs now more practical for use, but this technique of microstructure analysis can also be readily applied to other materials. Microstructures can be designed-to-order depending on the desired qualities in the material, which opens up a wide horizon for future applications of the technology. Sarac, who co-authored the paper, recently obtained his PhD from Yale with the completion of this project and is continuing his study in Germany on BMGs and their properties. At Yale, Schroers and his team are investigating flaw tolerance of metallic glass heterostructure as an analogous system to microstructures found in nature. Studying optimization of microstructures via the novel “artificial microstructures” technique in a lab setting could reveal new information about how nature optimizes its microstructures.
This research, uniquely situated in the intersection of the artificial and the natural and past and future of materials, has the potential to change materials from being limiting factors for innovation to being in the forefront of innovative construction and production.
About the Author: Deeksha Deep is a Sophomore Molecular Biophysics & Biochemistry major in Morse College. She is on the business team for the Yale Scientific Magazine and the beat editor for the Yale Journal of Public Health. She works in Professor Spiegel’s lab studying cell surface reconstruction in bacteria and vaccine design.
Acknowledgements: The author would like to thank Dr. Baran Sarac for his time and for his enthusiasm about his research.