“The Robot” dance is all about restricted, unnatural motion. Robotic systems are often mocked for their painful inability to comprehend nuance or intent in logical rules. In the Star War’s universe, AT-ATs move inexorably forward, yet are tripped up for their inability to adapt. Robots, in our fiction and in our factories, have always been rigid. Yet emerging research in the field of soft-robotics hints that truly flexible robots could be on the horizon.
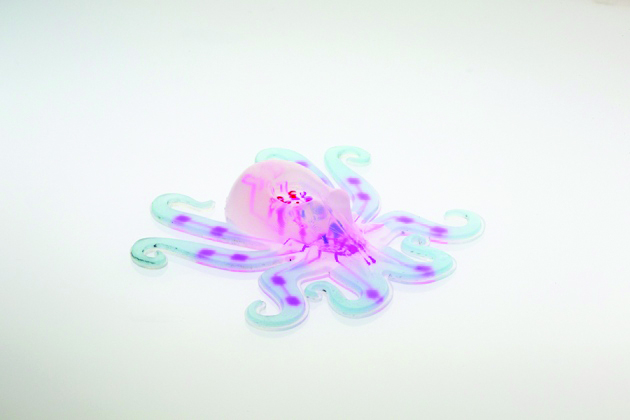
This harbinger of soft-robotics, the Octobot, looks like a children’s’ toy. It is a squishy, colorful plastic octopus, about the size of a pack of gum. It even waves its arms in a rudimentary dance. Yet this friendly fellow, designed at the Wyss Institute for Biologically Inspired Engineering at Harvard University, is a proof-of-concept grown from years of research that could revolutionize the ways we can use robots. The design was not a mere accident, but an homage to the animal it resembles. “We knew early on that this would be a legged system. We do not claim to mimic the behavior of the complex creature, but because it serves as an inspiration for the entire field of soft robotics, we wanted to use this form as a tribute to the endlessly fascinating creature,” said Michael Wehner, a research fellow at Wyss and co-first author of the paper.
Before the Octobot, the best soft-robotocists could hope for was a soft-shelled robotic system containing traditional silicon and metal circuitry, or a soft robot tethered to an external battery. Traditional power supplies and logic circuits are always made of hard materials, which is why the Octobot required massive innovation. The Octobot is constructed from entirely soft components and is autonomous. To accomplish this, designers utilized a pressure-based hydrogen peroxide circuit instead of a traditional electrical circuit and power supply; instead of electricity powering the Octobot, rising gaseous pressure pushes the action forward. The research team, led by professors Robert Wood and Jennifer Lewis, has been working on the Octobot for about three years, perfecting its imaginative fuel system, logic circuit, and fabrication.
Researchers fabricated the Octobot using cutting-edge 3D-printing technology. Previous methods of 3D printing could not fulfill their needs: Soft sensors and circuits are notoriously difficult to manufacture and involve labor-intensive production and multi-step insertion into the robot. But Ryan Truby, a graduate student at Wyss and the other first-author of the Octobot paper, led Professor Lewis’s lab to pioneer a new technology called embedded 3D-printing (EMB3D). EMB3D uses conductive carbon-based inks to draw circuits into silicon, using a needle-based setup reminiscent of a tattoo gun. The conductive ink can carry electricity like wires, but in this case, it is embedded with a slight tunnel to enable gas to travel. With EMB3D, Octobot researchers could draw-in circuits after finishing the main body piece, enabling precise, smooth lines to form the Octobot. Wehner intially had doubts about the Octobot design, citing difficulties in manufacturing, but according to Wehner, “Ryan [Truby] was confident that he could build what we needed. Together, we moved forward to develop the Octobot.”
The Octobot could not run on traditional electrical power, since that would require hard components. So researchers turned to the microfluid logic circuit, a circuit developed by Wyss professor George Whitesides that relies on pressure instead of electricity. Within the circuit, a slow chemical reaction converts liquid hydrogen peroxide into hydrogen and oxygen gases, creating a pressure from the gas that inflates channels in the Octobot’s legs. The logic circuit acts like a road map, and allows the Octobot to move a certain set of legs at a time, based on the pressure. The peroxide is stored in two reservoirs, and when it comes in contact with platinum embedded in the circuit, the peroxide turns to gas in a typical redox reaction. Separate channels direct the gas to the different limbs of the robot, allowing it to perform its dance.
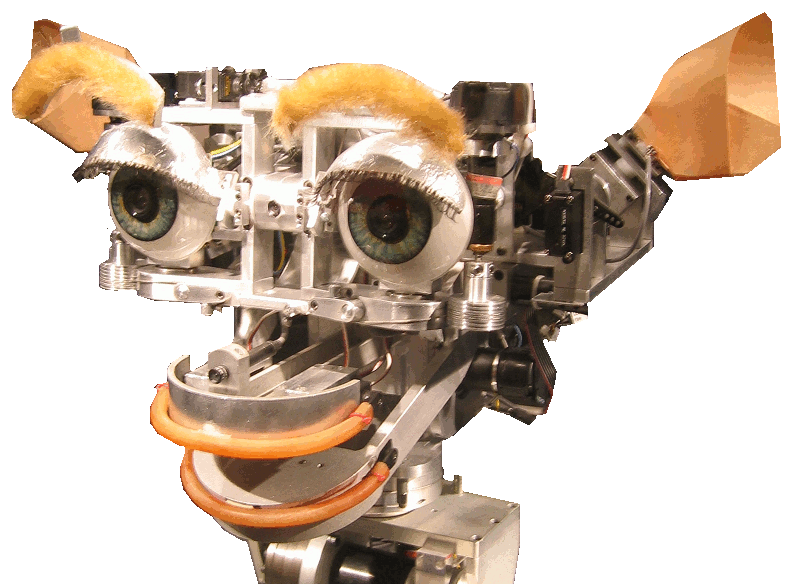
The logical channels are analogous to wires, and the fuel reservoirs similar to batteries. The channels in the microfluidic logic were 100×100 micron, compared to electrical circuits which can be built 1000x smaller. Wehner compared the fueling process to filling a car’s gas tank: “We have a supply of the hydrogen peroxide fuel. We attach two tubes to the Octobot, fill the Octobot with fuel, and finally remove the tubes. When the bot is empty, it can be refilled using the same process.” The Octobot can run for approximately eight minutes on one milliliter of fuel. While this seems like a small capacity, it is actually large and cumbersome when compared with electronics; the channels in the microfluidic logic are 100×100 micron, compared to electrical circuits which can be built 1000x smaller.
The current circuit is simple, so the Octobot’s motions are not very precise. When pressure builds up in one half of the circuit, it triggers the reaction in the second half. The Octobot exists in one of two states, with one half of its legs ‘raised,’ or the other, depending on the pressure from its fuel reservoirs. Creating more complicated soft-robots using this technology will be no small task, but Wehner is confident that the soft-robotics community is up to the challenge, since there have been large community advances in embedded systems. “One of the primary advantages of this fabrication technique is that it allows embedded microfluidics…We hope that in addition to our future efforts, the rest of the community will use this approach to build novel devices that we can’t even imagine.” At this time, the Wood and Lewis labs plan to continue collaborating but are open to other partnerships. “We love working with others. It is the best way to develop even more complex systems and learn even more than we could alone,” said Wehner.
The Octobot is a triumph for soft-robotics, but it is not a solution. In order to create an Octobot that can perform complex tasks, researchers must overcome space constraints, increase the complexity of the logic circuit, direct the gas release more precisely, and speed up the peroxide circuit—which is currently quite slow. The team at Wyss is already at work improving the Octobot to incorporate sensors and a more precise control strategy. They hope to generate more sophisticated behavior and even create a soft robot capable of reacting to the environment.
But for now, this cute little harbinger is content to keep dancing.