Spongebob is weak; therefore, he cannot lift a marshmallow dumbbell. This logic seems sound because it is grounded in the public’s perception of sea sponges as little more than mush. While it is fine for Nickolodeon writers to exploit this view, it would be unwise for engineers to hop on the bandwagon. Bioinspired science teaches us that nature’s ingenuity manifests itself in unusual ways. Madhusudhan Venkadesan, assistant professor of engineering at Yale University, believes that the natural world and its vast applications should be a primary inspiration for engineers. “All of [these applications] inspire us to learn a little more about other organisms on this planet,” Venkadesan said. If the beetle you just squashed underfoot can inspire titanium suspensions for military vehicles, why write off squishy sponges?
As it turns out, sponges aren’t so soft after all. Bundles of silica rods called strongyloxea spicules are located within the body of the orange puffball sea sponge, Tethya aurantia, to help it maintain its form. In the ocean, where sponges are not only subject to currents and tides, but also must pump moving water through their bodies, structural integrity is of paramount importance. Brown University engineers Haneesh Kesari and Michael Monn started to uncover these sponges’ strength when they noticed the consistent shape of the spicules: always about two millimeters in length and tapered evenly at both ends. By measuring spicules and comparing them to a mathematical model, Kesari and Monn found evidence to suggest that the spicules were ideally suited to resist buckling, which gives them major potential for applications in architecture, transportation, biomedical engineering, and other important fields.
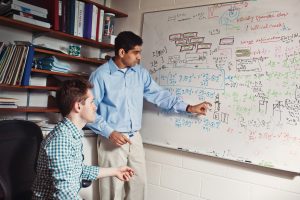
It is unsurprising that sponges have developed the perfect support system. After over seven hundred million years of evolution—trial and error, if you will—sponges were bound to stumble upon the optimal spicule by random chance and variation alone. Spicules serve a single function, whereas human bones, for example, have many functions—anchoring muscle, making bone marrow, and maintaining our shape—so spicules had a better chance of taking a form that suits exactly what they do. As Kesari related, it is as though sponges have had to pick only a handful of winning lottery numbers throughout their long evolution, whereas humans have had to pick hundreds in a fraction of the time. As humans and as engineers, it is easy to assume that we are the smartest and make the best structures. “We don’t appreciate the simplicity through which nature can arrive at same conclusions,” Monn said.
Once Monn and Kesari noted the consistency of the spicules, the researchers investigated their purpose through the lens of an engineer. Venkadesan remarked that lots of successful bioinspiration stems from salient observation of an organism’s form or motion that is then applied to engineering. By developing a structural mechanics model, or a model of the forces acting on an individual spicule, the Brown team determined that a load applied to a sponge would compress its spicules from both ends, instead of causing them to buckle and break at the center, which happens in similarly shaped, slender columns. Bioinspired designs often overlook this structural property in favor of toughness, the ability of a material to break gradually rather than all at once. Spicules stand out because in the context of the natural world, toughness is not their most important quality. Kesari reflected that if engineers have preconceived notions of what specific properties a material should have, they risk overlooking its intended function and stagnating the field.
With buckling resistance in mind, the team took measurements of dozens of spicules to determine their shape and compare it to the “optimal column.” The Clausen Profile, a model of the perfect dimensions for a column, predicts that columns with tapered ends can better avoid buckling. The model dates back to the nineteenth century and has never been used in a practical application, so it took effort to dig up. Conforming to this model, and unlike other aesthetic columns in the engineering world, spicules are tapered in precisely the right way to maximize their buckling resistance. Compared to an untapered column of the same length and volume, spicules can withstand thirty-three percent more compressive force—a significant difference. “[We’re] linking this previously known shape to designs that are practical,” Monn said. Although Venkadesan warns against replicating an observed form in exact detail without consideration for what sort of function it achieves, spicules’ relevance is broader. Even without adopting the exact shape, the engineering foundation behind spicules can be used to improve material design across a variety of fields.
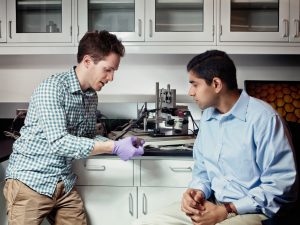
Now understanding how to approach the design of slender columns, the team can combine their findings with the best materials to supersede the engineering of the natural world. They break down potential applications of their work into three categories. The first is on a micro-scale and would be used mostly in the context of medicine. Integrating a tapered structure into products such as needles, catheter guide wires, and arterial stents would help them be be as unobtrusive as possible, minimizing surgical incisions but maximizing support.
The second use is larger-scale stationary applications, such as trusses, or the frameworks that support, say, a skyscraper or a bridge. An optimally slender truss will save weight and material. Kesari relates this idea to packing boxes: of course, cement works best if the only condition is that the box cannot break, but cardboard strikes a much more attractive balance between retaining its shape and being light enough to carry. Beyond building a more economical truss, this innovation will introduce a new failure mechanism against buckling, which, if unaccounted for, could pose a major problem on this scale.
However, the area where the team sees the most potential is in transportation. Implementing better materials is critical in this field because performance remains important with every trip. Beyond more efficient construction, from which a static structure would also benefit, a tapered column could cut fuel costs and has incredibly attractive economic and environmental implications. This application is arguably the most ingenious and the most important in today’s world.
Although it is hard for revolutionary designs to overtake the default, Kesari and Monn believe that there is reason enough to make the principles behind the spicules’ structure more widespread. They hope to drive radical changes in materials science. In the end, it would be a shame if squishy sponges showed potential to be stronger than Larry the Lobster and the engineering world failed to capitalize on it. Spongebob simply would not forgive us.